blog | edge computing
Unleash Predictive Maintenance in IoT with Edge Computing: The Key to Increase Efficiency and Reduce Costs in Industry 4.0
Long life to IoT sensors
Predictive maintenance is a critical component of Industry 4.0 that helps organizations fix issues before they cause downtime with its proactive approach that uses real-time equipment performance tracking and data analysis to predict machine failure.Β
IoT is a key part of the Industry 4.0 strategy, which works to create flexible and connected digital factories where communication is facilitated between all parts of the system, and it combines with AI, ML, and robotics to digitize manufacturing.Β His role is critical, as it enables the monitoring of production systems in manufacturing and services, facilitates higher performance, and creates innovative possibilities in manufacturing by collecting and sharing information with the help of internet-connected machines and devices.Β
IoT sensors gather data about different parameters such as temperature, vibration, humidity, light, etc. This data is then analyzed to predict when a failure may occur, and maintenance is performed only when it is actually required, helping businesses avoid unnecessary expenses, allowing maintenance to be scheduled before the failure happens.Β As a result, it canβ―increase productivity by 25%β― and Β lower maintenance costs by the same amount, according to estimates quoted by Deloitte.Β
The Role of Edge Computing in Predictive MaintenanceΒ
Edge computing allows IoT to perform smart automation and predictive maintenance, optimize the data lifecycle and, therefore, reduce costs.Β
Related to data collection, in some cases, this is done on an hourly or daily basis or only when triggered by a specific interaction with the device. Edge computing can provide a benefit to IoT when these insights are needed in real-time.β―Β
For β―IoT automation solutions, AI-generated ideas in the cloud are sent back to the field to induce some action. However, this approach lacks speed and throughput, which becomes critical for widely distributed architecture and a large amount of data that needs to be processed. This is where intelligent edge devices come into play, taking on processing, analytics, and action. Their benefit is revealed through their proximity to the data source allowing them to reduce latency through the delegation of some basic decision-making credentials to them.Β
Benefits of predictive maintenance in Industry 4.0
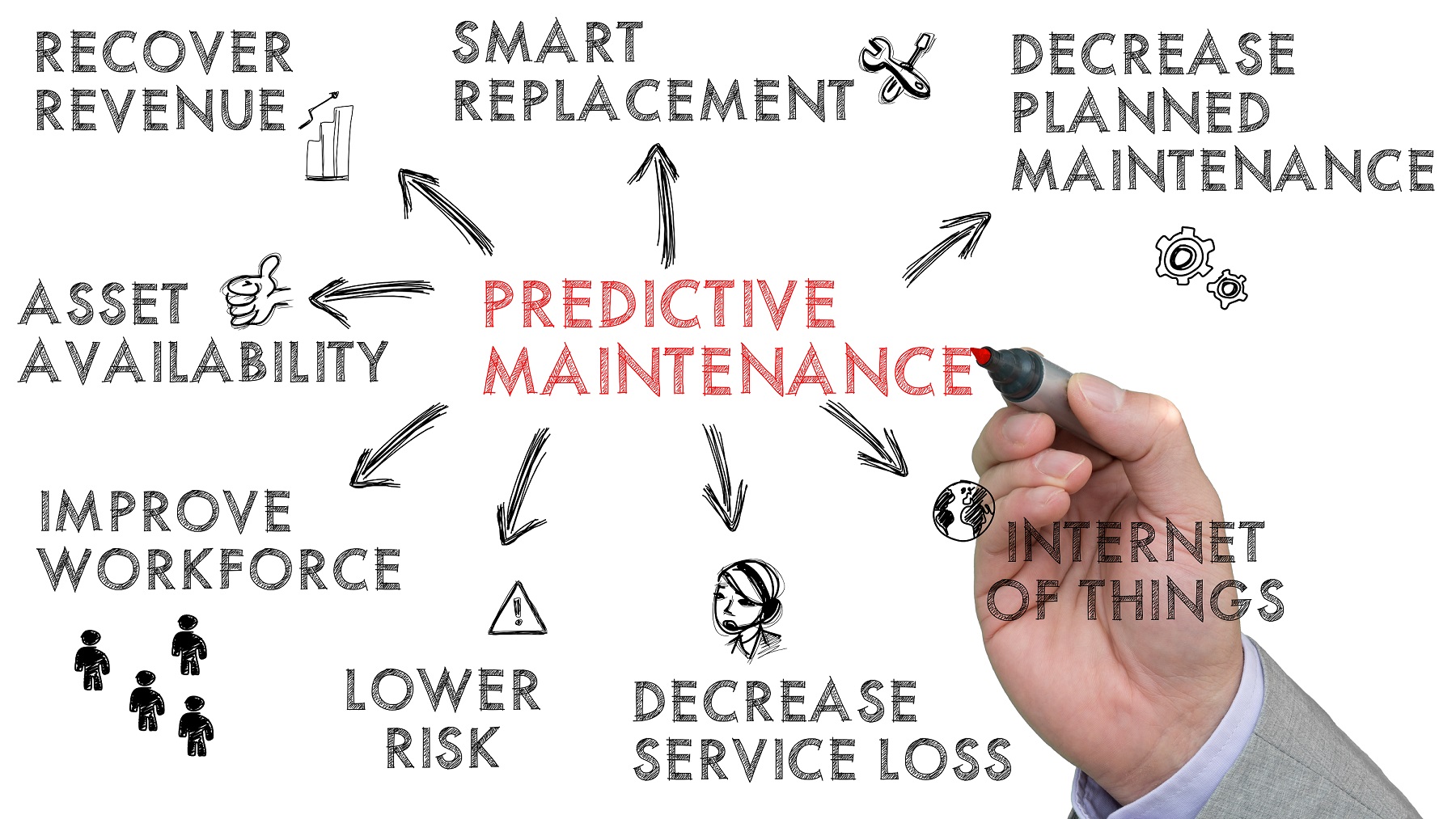
Figure 1. Predictive Maintenace. Other benefits
- Reduced maintenance costs: Predictive maintenance can reduce maintenance costs by cutting down on premature maintenance that is largely wasteful, leading to a tenfold return on investment in some cases.Β
- Reduced downtime: Predictive maintenance can reduce unplanned downtime by catching issues before they become serious, improving production yield and reducing the risk of equipment failure.
- Improved equipment reliability: Predictive maintenance can improve equipment reliability by detecting and addressing issues before they cause equipment failure.
- Increased safety: Predictive maintenance can increase safety by reducing the risk of equipment failure and ensuring that equipment is operating as intended.
- Improved product quality: Predictive maintenance can improve product quality by reducing product defects and thereby eliminating waste.
- Real-time insights: Predictive maintenance provides real-time insights into equipment performance, enabling proactive decision-making and reducing the risk of equipment failure.
The Role of Edge-to-Cloud Orchestrator Platform in Predictive Maintenance
In the context of predictive maintenance for IoT, edge-to-cloud orchestrator platform plays a critical role in enabling real-time data processing and analysis at the edge of the network. By deploying machine learning models and other predictive analytics algorithms on edge devices, it is possible to analyze sensor data in real-time and detect anomalies or patterns that may indicate a potential failure. This enables maintenance teams to take proactive measures to prevent equipment failure, rather than simply reacting to failures after they occur. Implementing and Edge-to-cloud orchestrator platformΒ as NearbyOne as part of the enterprise digital transformation,Β Β enables the deployment of predictive maintenance applications across a distributed network of devices, which can be challenging to manage manually. By automating the deployment and management of edge platforms, it is possible to ensure that predictive maintenance applications are running smoothly and efficiently across the entire network of devices.Β